Written by Ben Ruchte, P.E., Director of Product Engagement
The pursuit of precision and the quest for deeper insights have been constants in ferrous-based components’ metallurgy and failure analysis. Traditional methods have served admirably, but in this age of advanced technology, is there a crucial element missing in the standard toolkit? Enter Micro X-ray Fluorescence (microXRF) technology, a powerful and versatile analytical tool that has the potential to bridge the gap and unlock a new dimension in the analysis of ferrous-based materials.
The Conventional Approach
Metallurgists and engineers have long relied on established metallographic techniques for preparing their samples for analysis via optical microscopy, electron microscopy, and X-ray diffraction to characterize the respective materials (Figure 1). These methods offer valuable information about a sample’s composition, microstructure, and defects. However, some limitations have left experts seeking a more comprehensive solution.
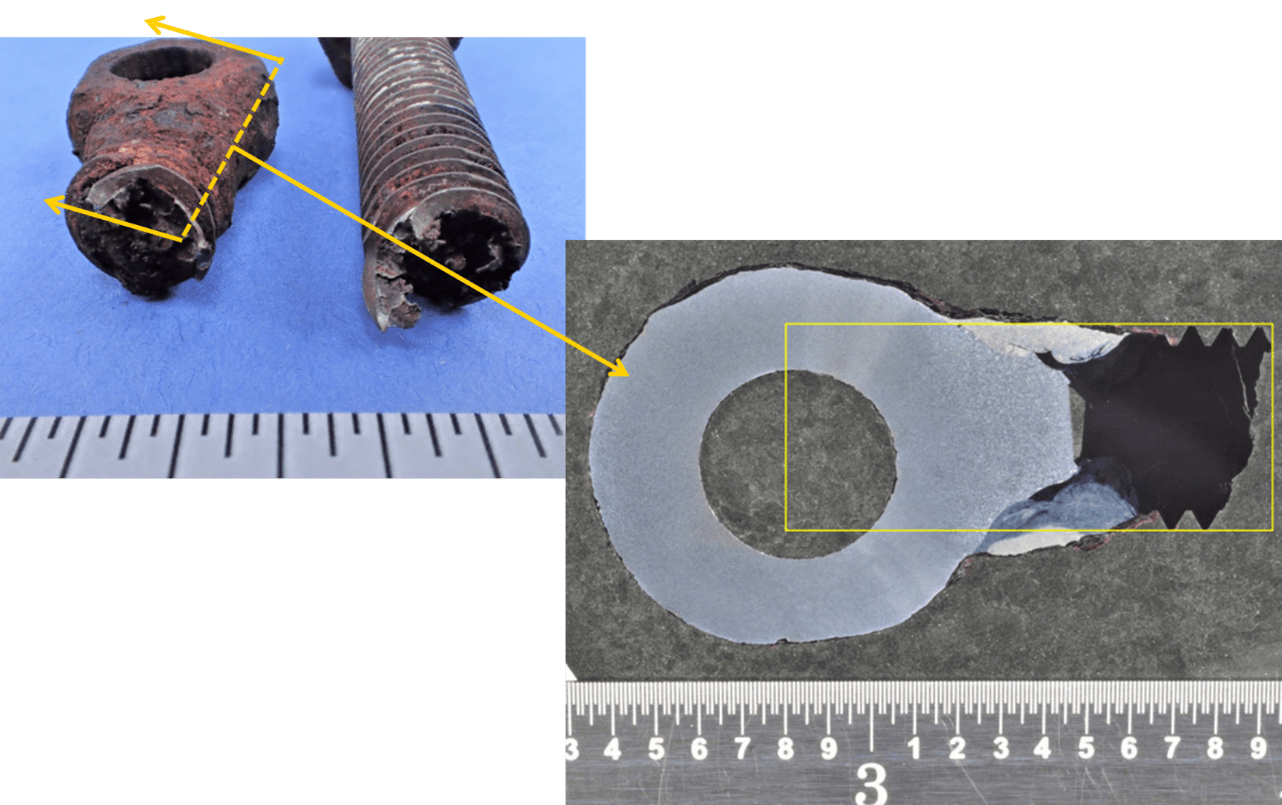
Figure 1. [Upper Left] Views of a fractured gland follower bolt as received for analysis. The fracture occurred in the threaded portion of the bolt just above the knuckle. [Lower Right] Cross-sectional view, captured via digital microscopy, of the fracture surface from the knuckle side of the bolt. Cross-sections are prepared via standard metallographic techniques that reveal pertinent microstructural information about a sample. This cross-section reveals that a threaded stud had been welded to the knuckle and that the stud and the knuckle were different materials. The yellow box illustrates the general position and orientation of the stud relative to the hole in the knuckle. Notice that the stud is offset from the hole (Etchant: Nital).
MicroXRF As A ‘Disrupter’
MicroXRF technology offers a fresh perspective on the analysis of ferrous-based materials, bringing with it a host of benefits that address the limitations of conventional techniques.
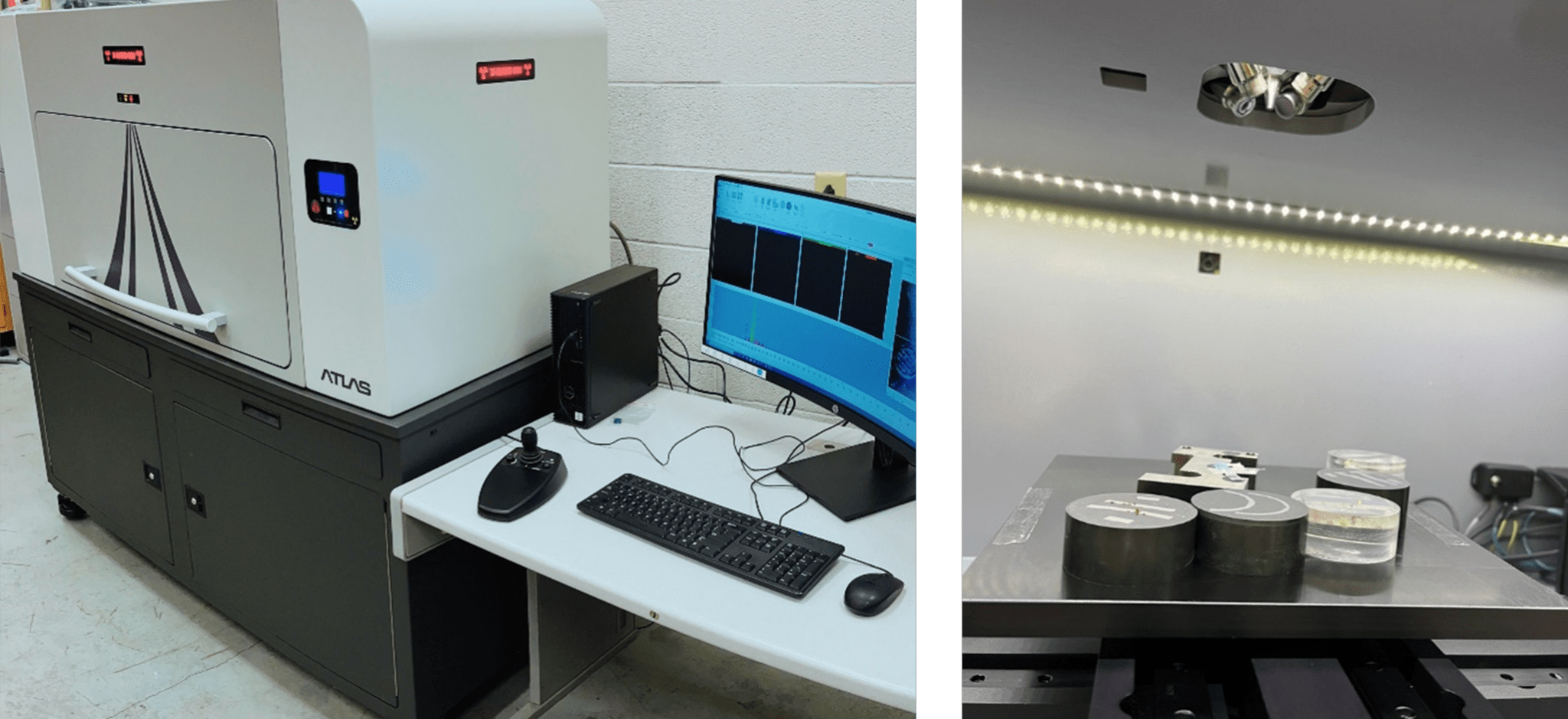
Figure 2. [Left] Picture of Atlas X microXRF from IXRF Systems. [Right] View of samples mounted on the Atlas XYZ stage before acquisition.
Elemental Analysis Without Losing Spatial Resolution
MicroXRF provides insights into the distribution of elements within a sample. This capability is especially significant when investigating the localized variations in composition, microstructure, and defects within ferrous components. Enhanced spatial resolution using microXRF offers the precise location of elements within your sample down to 5–micron spacing. This is particularly useful when pinpointing an element’s exact location or when dealing with samples exhibiting high heterogeneity (e.g., corrosion, micro-segregation, etc.). Polycapillary optics allow researchers to identify areas of interest with remarkable accuracy and can serve as a valuable preliminary step for more detailed analyses, such as scanning electron microscopy when required.
Non-Destructive Advantages
Unlike some conventional techniques that require destructive sample preparation, microXRF is non-destructive. This means that the sample’s integrity is preserved, allowing for further investigations or archiving for future reference. It’s a crucial advantage when dealing with rare or irreplaceable components. This is also important as it has the potential to augment, reduce, and even replace steps when performing a failure analysis/metallurgical condition assessment (see Figure 3).
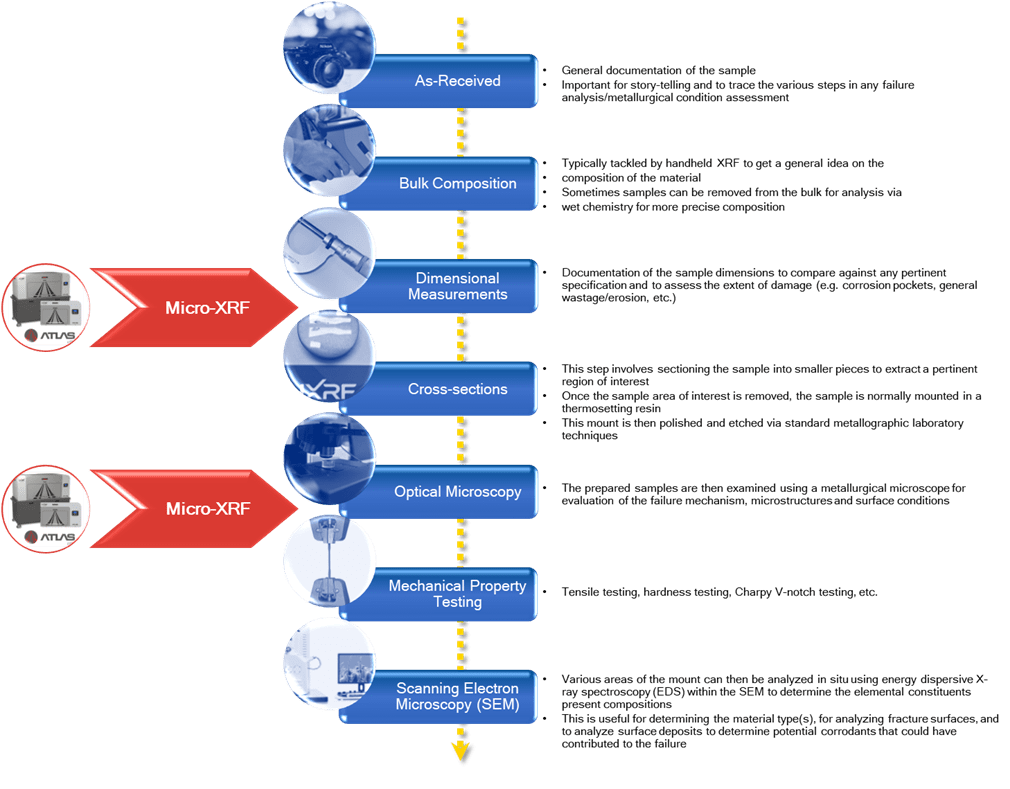
Figure 3. Flow chart shows common steps in evaluating ferrous-based components and the potential ‘disrupter,’ microXRF, to a process that has mostly remained unchanged since the 1950s.
Large Area Scanning
MicroXRF excels in scanning larger areas compared to some other analytical methods. This is particularly advantageous as ferrous components can have simple or complex geometry, such as large structural parts, ensuring no critical information is missed. Additionally, samples can weigh as much as 10kg!
Sample Environment Flexibility
MicroXRF instruments offer the flexibility to analyze samples in various environments, including air, inert gas, and vacuum. This adaptability ensures that the analysis conditions can be tailored to the material’s specific requirements to optimize pertinent element sensitivity.
Enhanced X-ray Sources
One other remarkable advantage of microXRF technology is the enhanced X-ray sources it employs. These sources are generally much more powerful, with up to 50 kV and 1000 uA capabilities. This increased power enhances the depth and precision of analysis, allowing for more accurate measurements and detection of trace elements. Compared to traditional methods like energy dispersive spectroscopy (EDS), which are employed within the SEM, microXRF offers distinct advantages tied to the ionization cross-section theory[1]. The ionization cross-section measures the probability that a given ionization process will occur when an atom or molecule interacts with a photon (σ) or electron (Q). Electron excitation becomes less favorable with increasing atomic number (Z) – as shown in Figure 3 and Figure 4.
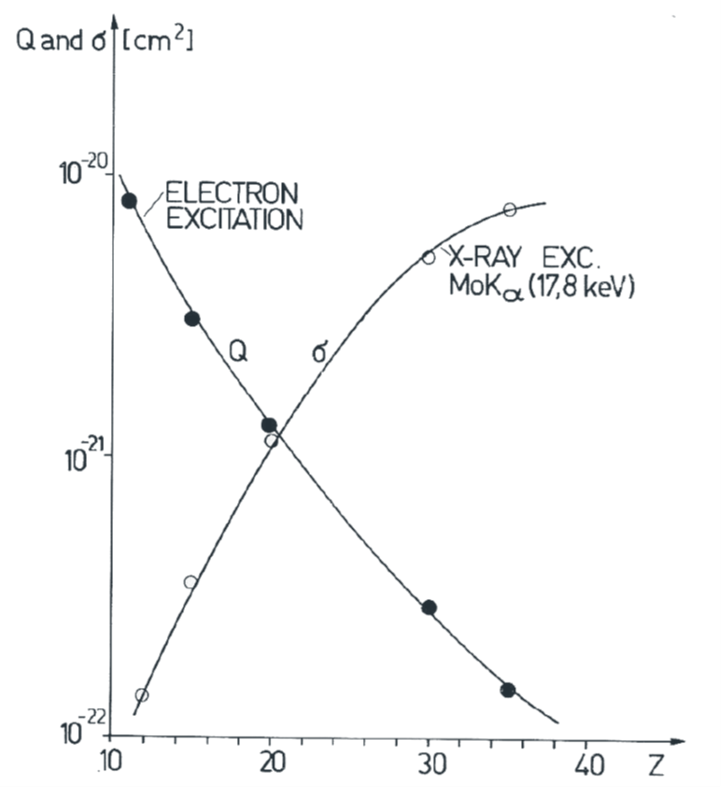
Figure 4. Plot showing the favorability of excitation via photons or electrons with increasing atomic number (Z).1
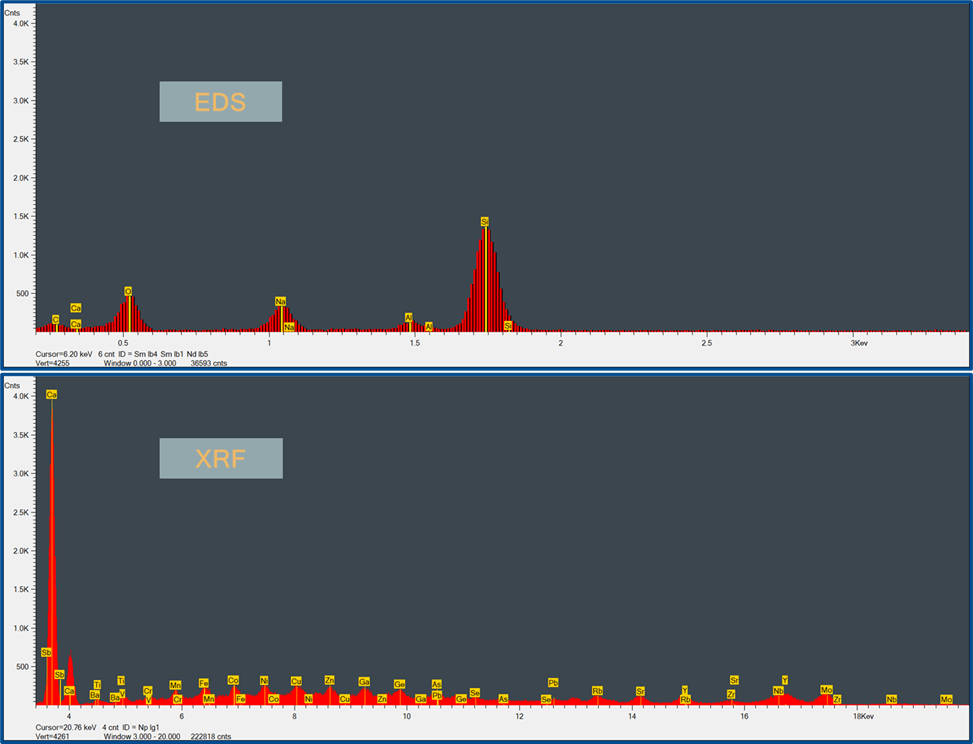
Figure 5. Spectra of NIST 610 glass show XRF’s prominence at eliciting trace elements beyond 3 keV – these elements were not discovered with EDS.
The Missing Link?
So, is microXRF technology the missing link in standard metallurgical and failure analysis of ferrous-based components? Its ability to provide insights that complement and enhance existing techniques is powerful. While it may not replace traditional methods, it undoubtedly fills a vital role in the toolkit of materials scientists, metallurgists, and engineers.
In conclusion, microXRF technology is poised to usher in a new era of precision and thoroughness in analyzing ferrous-based components as a true ‘disrupter.’ Its unique capabilities, including high spatial resolution elemental mapping, non-destructive analysis, the ability to scan larger areas, and the utilization of powerful X-ray sources, make it a valuable addition to the repertoire of tools used in metallurgy and failure analysis. As technology advances, so does our capacity to uncover the intricate secrets hidden within the very materials that power and support our world.
IXRF Systems is a leading provider of X-ray fluorescence instrumentation. With our advanced analytical solutions, we are committed to supporting research, quality control, and educational endeavors across various industries.
1Pozsgai, I. (1991). X-ray microfluorescence analysis inside and outside the electron microscope. X-Ray Spectrometry, 20, 215-223.